Smart Factory
Smart Factory
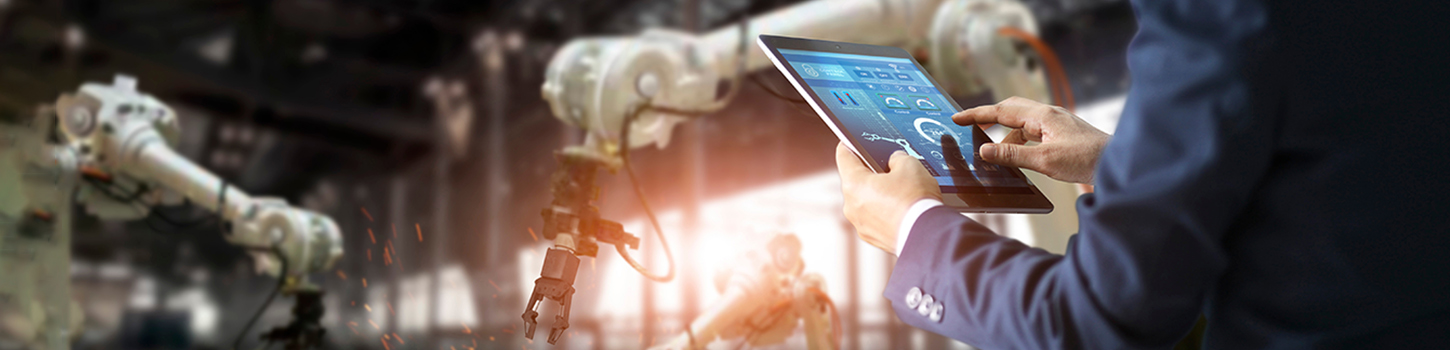

WeZON's Smart Factory is a factory that can self-monitor and -control based on real-time data collected and analyzed through
sensors installed on equipment and machines(IoT) with clear visibility of the factory’s operation.
In response to the ‘Smart Factory Support Project’, the government supported the completion of 30,144 Smart Factories until 2022 and
the companies that adopted smart factories have achieved increased employment and improved productivity.
WeZON is a company that has already been registered in the pool of suppliers in the Smart Factory promotion group and our goal is to grow
together with companies in demand by providing stable services ranging from consulting and system establishment to post-management
based on our experience of over 20 years in supplying industrial IT solutions.
Please contact us if you are a company with plans to ‘build and upgrade new smart factory-related systems.
Introduction of
Smart Factory
An intelligent factory in the 4th Industrial Revolution era that enables data accumulation and utilization in manufacturing process,
production, and delivery management
Performance of
companies that
adopted
Smart Factory
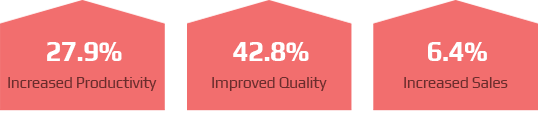
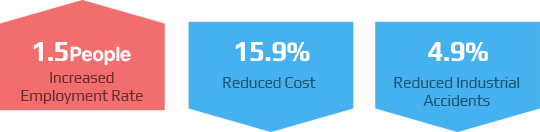
Smart Factory
supply and
distribution
status
Smart Factory
adoption inquiry
process & method
Smart Factory
adoption inquiry
Counseling and
on-site inspection
by WeZON consultant :
Establish construction plan /
Total project cost estimate
Decide optimal support business type
(New/Advancement)
Prepare business
plan (WeZON)
and project support
Install Smart Factory
after the selection
Stabilization and
post-management
Smart Factory
project vision
Our goal is to grow together with our customers “as the world’s top-class
software solution company in the plant & production field within 10 years.”
We will focus on providing integrated systems in the manufacturing and environmental fields and on improving the ease of use.
By gradually ‘adding and expanding’ various solutions or functions, the data will be easily linked(API provided)
and conveniently used as a single system in the future.
Introduction to
supportable solutions
Factory
Management Suite
We provide “Factory Management Suite” based on equipment production management and quality process monitoring.
Product inquiry
02-555-7401
smart@wezon.com
Manufacturing Execution System
WeZON MES: Production management system
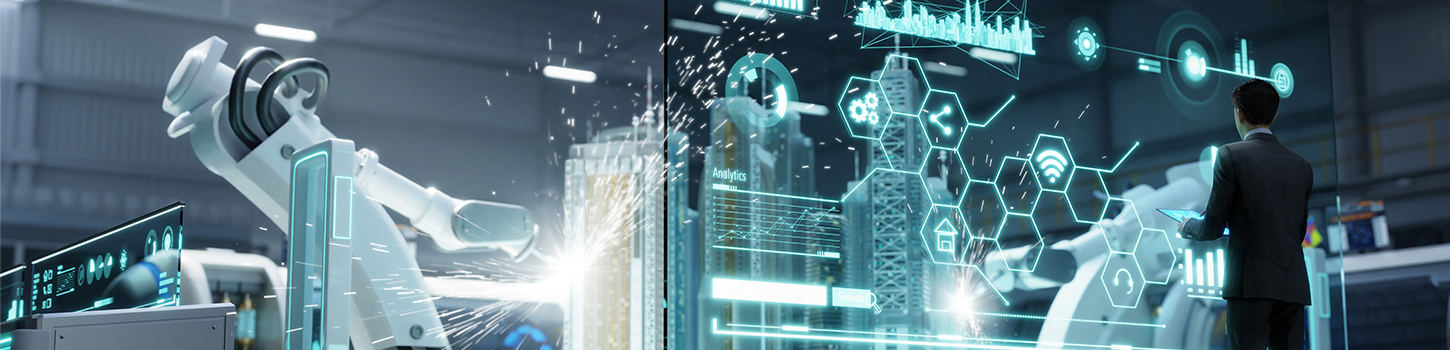

WeZon's integrated production management system(Manufacturing Execution System, MES) aims to optimize operations by recording
and integrating data created during material purchasing, production planning, and process work at the factory site.
It is not just a tool for planning, but an execution system for controlling and managing the actual manufacturing process and work progress.
WeZON MES
On-Premise
based production
management solution
MES is not just a simple field information collection software, but an integrated production management system that accompanies
companies on their journey to build a successful Smart Factory.
WeZon MES obtained GS certification level 1 in June 2022, and it is supplied to small and medium-sized manufacturing companies.
Key functions include production planning, material management, real-time process monitoring, quality operations,
and resource allocation and control.
Importance
-
01
Supports connection and integration
Supports connection with legacy systems and integration of various communication protocols
-
02
Provides industry-specific solutions
Provides industry-specific MES solutions applying SW development know-how of over 20 years of business experience
-
03
One-stop service throughout the entire process
Provides one-stop service throughout the entire process from field analysis – consulting – design – construction that reflects
the characteristics of each industry -
04
Project implementation and Korean Standards Association partner
Implements multiple projects to spread Smart Factory supply and is a partner of the Korean Standards Association
Key functions
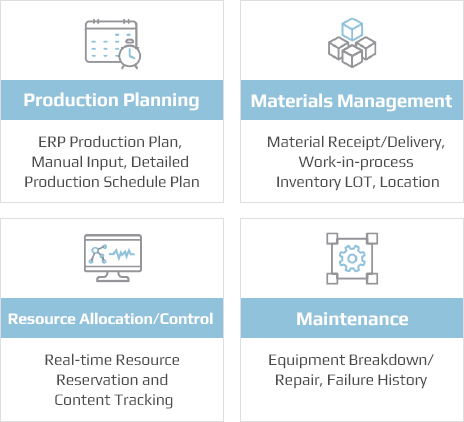
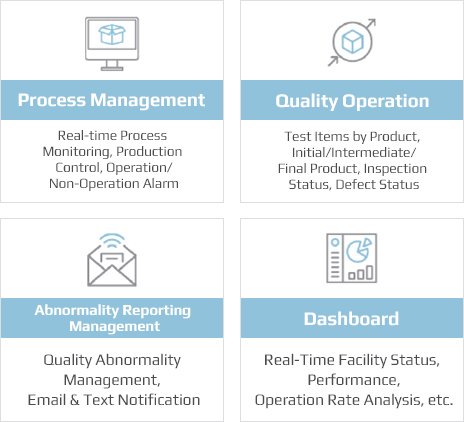
Expectations
-
Systematic work plan(Weekly/Monthly)
Secures flexibility in production plans according to customer orders and ordering plans
Check equipment/manpower/material availability
-
Check real-time manufacturing site production information
Improves production information accuracy/speed
Real-time check of production progress compared to branch
Improved quality through quick identification of defects/abnormalities
-
Quick work order confirmation
Quick response to emergency production, changes in work details, etc.
Supports quick sharing
-
Reduces paperwork
Reduces computer input time through real-time data collection and automatic analysis
Automatic generation of statistics reports on comprehensive equipment efficiency
Increased work efficiency by automating performance input
MES for Smart
HACCP
Smart HACCP
solution for food
safety management
Integrated with ICT technology, Smart HACCP management system achieves quality assurances with collection/management/analysis of data,
which include digitizing all the data produced during the manufacturing process and automating the monitoring of important control points
and key processes.
Process
Key functions
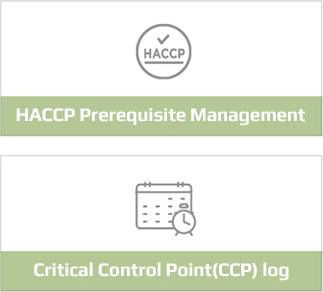
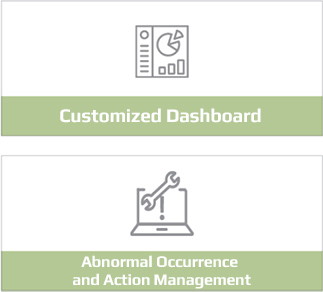
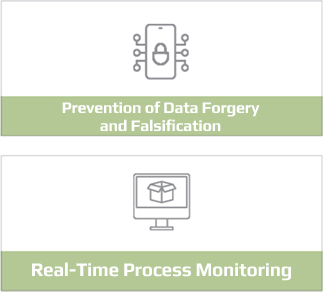
Product inquiry
02-555-7401
smart@wezon.com
Computerized maintenance management system
SWING CMMS : Equipment management system
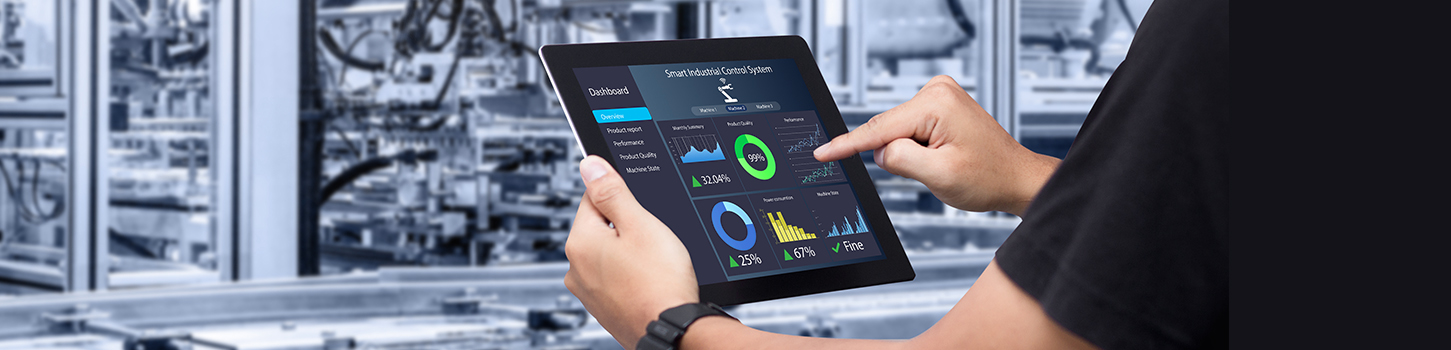

WeZon SWING CMMS is equipment asset management software for equipment maintenance personnel and equipment management departments.
SWING CMMS is a system developed to suit realistic situation by incorporating the advantages of advanced maintenance work processes(Best Practice)
Even users who are not familiar with the system can easily begin systematic equipment management tasks
Importance
-
01
Convenience of use
Work can be processed with multiple work screens displayed at once
Additional advanced search can be used in addition to basic search conditions
Additional advanced search can be used in addition to basic search conditions
Search function for help on key information, and hash tags
-
02
Supported services
Provides templates for preparing standard information and preventive maintenance schedules
Provides templates and guides for organizing past maintenance history
Supports optimized scheduling of establishment procedures to minimize on-boarding time
* Migration of preventive maintenance master and maintenance history data other than standard information is optional
-
03
Connection and expansion of related systems
Connected with existing legacy systems(HR, SSO, etc.)
Expansion of equipment status monitoring and predictive maintenance solutions
Data collection on the status(temperature, pressure, vibration) of key equipment
It supports the establishment of an instability prevention maintenance process through Planned vs. Unplanned Task management,
and provides basic support for uploading and verifying standard information and user training to minimize system on-boarding time
In addition, it provides a solution for real-time collection of on-site equipment status data, supports on-site installation(construction)(optional)
manages equipment status alarms, and can be used as data for predictive maintenance based on accumulated data.
Process
Key functions
Work request, order and history management |
---|
When equipment abnormalities are discovered, quickly normalizes equipment through work requests, work orders, and history management |
Confirmation and management of equipment & maintenance material information |
---|
Easy checking of basic information such as basic specifications, location and quantity, and price of equipment and maintenance materials |
Report and statistics |
---|
Generate various reports and is easy to check statistics such as maintenance costs by equipment, work compliance rate by department, preventive maintenance rate, preventive inspection performance rate, etc. |
Preventive maintenance & inspection plan |
---|
Establishment of preventive maintenance and inspection plans for each facility using a calendar, and efficient maintenance activities through a work list |
Status view(Dashboard) |
---|
Check the status of facilities and work status at a glance, and manage related data |
Expectations
Enhanced equipment
management
-
Enhanced equipment operation rate
Prevents unexpected failures by analyzing maintenance data such as equipment down time,
number of failures, and working hoursReduce accident rate through preventive inspection for repetitive defects
-
Reduction in maintenance costs
Reduced logistics and inventory costs for repair materials
Reduced emergency purchase of repair materials Reduced purchase costs
Reduced excessive overtime Reduced overtime pay
Excludes inappropriate input from external service providers
-
Improved maintenance management structure
Strengthened collaboration within the factory through mobile apps
Real-time information sharing between multiple working level personnel
and approval authorities Quick/accurate decision-makingClear responsibilities and authority
Systematic accumulation and sharing of know-how through standardization of work procedures and methods
-
Facility asset management
Integrated management of facility asset information(Connected facility structure of location
and type supports efficient maintenance activities)Extended lifespan of facilities and parts through optimal management
Continuous improvement of the facility management process
Product inquiry
02-555-7401
smart@wezon.com
Equipment Condition Monitoring System
Equipment Condition Monitoring System(eCMS)
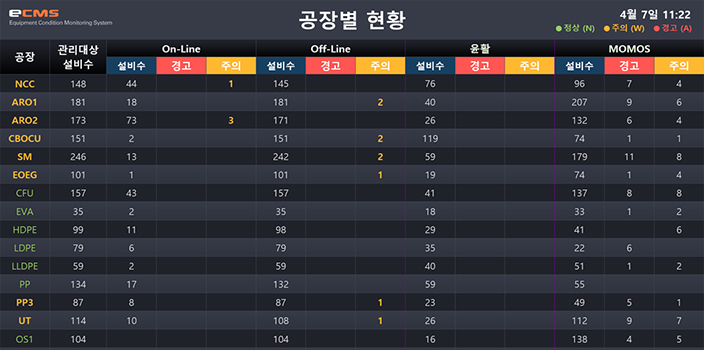
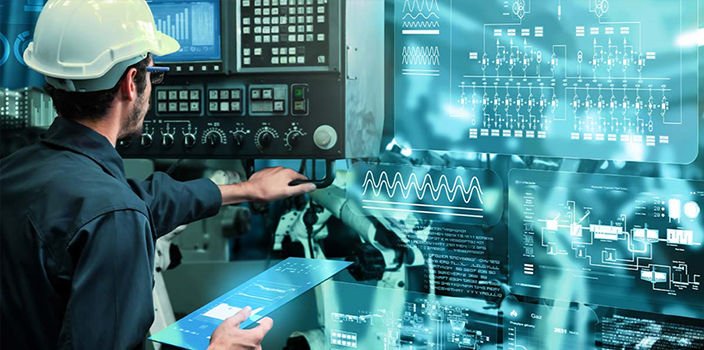

Integrated facility status monitoring system aims to improve work efficiency and to continuously improve facility availability by performing facility monitoring/alarm confirmation/reporting/knowledge sharing through integrated management of predictive maintenance data
Key products
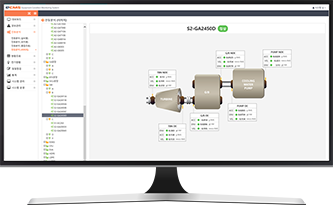
Imaging measurement data
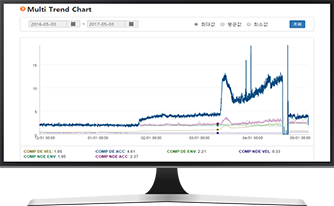
Vibration-Multiple trend
Importance
Data generated from various systems across the company exist in separate local systems in the process network,
making it difficult to utilize and share inspection results or past data.
WeZon's Equipment Condition Monitoring System(eCMS) is an ‘integrated system’ that integrates and links individual status monitoring
and periodic system data dispersed across the factory to efficiently process alarm confirmation, reporting, and knowledge sharing.
System
configuration
diagram
Key functions
Dashboard |
---|
Factory status |
Status by factory |
Alarm List(Facility) |
Alarm List(Location) |
Alarm List(Lubrication) |
Alarm List(Corrosion) |
Temperature status by channel |
Alarm List(Temperature)) |
Temperature status of entire factory |
Alarm List(PD) |
PD status of entire factory |
Alarm management |
---|
Vibration Alarm(By factory) |
Vibration Alarm(By equipment) |
Vibration Alarm(By system) |
Vibration Alarm history |
Lubrication Alarm history |
Daily inspection |
Daily report |
Weekly report |
Send report |
PM performance management(Weekly) |
PM performance management(Monthly) |
Vibration analysis |
---|
Vibration analysis(By equipment) |
Vibration analysis(By location) |
Vibration analysis(Integrated search) |
Vibration analysis(Image) |
Statistics |
Alarm occurrence status |
Alarm action status |
Equipment code matching status |
Vibration On/Off line status |
Status search |
---|
Lubrication analysis result |
MOMOS result |
Process load |
Corrosion monitoring status |
Electricity status |
Temperature monitor(By channel) |
Temperature monitor(By location) |
PD monitor status |
Expectations
-
Enhance work efficiency
Intuitive status identification through information integration and visualization
Share situations and reduce response time
Supports quick decision-making by reducing alarm/failure analysis time
Increased work efficiency and reduced human error through off-line system integration
Simplified work and reduced time through report systemization
nhanced members satisfaction level with workload reduction
Monitoring of actions managed through irrationality list and F/U list
Enhanced work satisfaction level and focus on improving safety/environment/health/process
-
Strengthened safety and protection posture
Accumulation of equipment fail history/diagnosis history and improved accessibility
Accumulation and sharing of equipment diagnosis knowledge
Company-wide synergy effect through knowledge sharing
Utilize internal training - Foster experts
Obtain the foundation for smart diagnosis laid through accumulation of diagnosis history
Sustainable knowledge growth
Product inquiry
02-555-7401
smart@wezon.com
Mobile Field Logging System
Mobile Monitoring System MOMOS
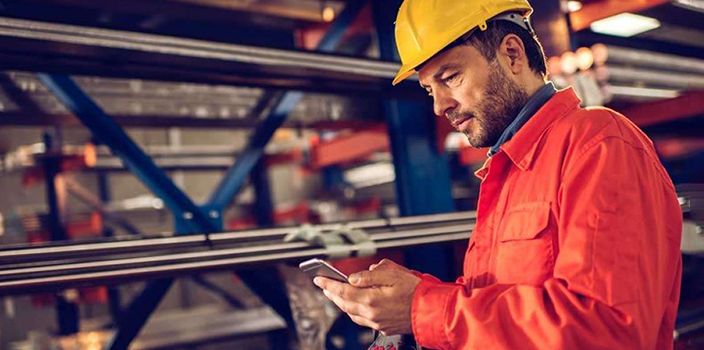
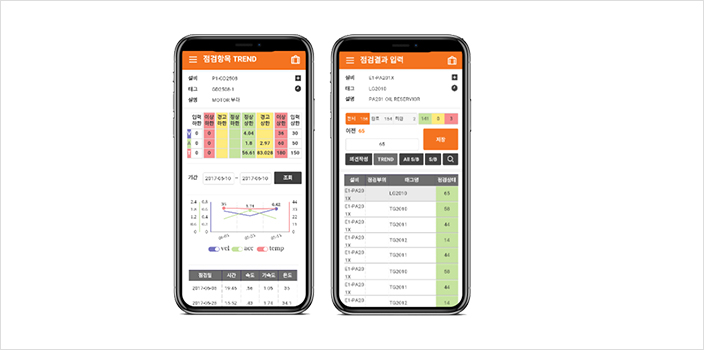

MOMOS connects mobile devices with vibration and temperature measuring instruments, automatically inputs the measured values from the measuring
instruments into the mobile device in real time, and performs inspection tasks to enable real-time sharing of equipment information and prevention of equipment accidents.
Importance
-
01
Mobile utilization
Various data measured in the field can be utilized online immediately.
-
02
Increased convenience of patrol work
During patrol work, information can be entered directly via mobile without having to write it manually on paper.
-
03
Reduce personal work load
Work overload is reduced through automation/computerization of inspection tasks, and field employees can utilize multiple data simultaneously.
-
04
Standardization of measurement results
Setting of legal inspection, equipment inspection, and operation inspection is feasible, as well as adjusting the inspection cycle.
-
05
Diagnosis of abnormal equipment becomes feasible
Setting legal, equipment, and operational inspection and adjusting the inspection cycle become feasible.
-
06
Utilization of data with other systems
By connecting with Yullin Technology's eCMS and SHE system, data such as equipment monitoring and statutory inspection targets can be shared.
-
07
Monitoring of the manager’s work status(KPI)
The implementation rate and non-inspection rate by task and inspection, as well as the inspection plan rate and inspection results by team and task can be identified.
Process
Key functions
Web Part | ||
---|---|---|
Dashboard | Inspection work | Equipment management |
Approval work |
Inspection history and plan |
Equipment abnormality management |
Basic work |
Inspection status |
Equipment/inspection, |
Shift journal |
Search inspection sheet |
|
Work assignment |
Bulletin board | My Page |
Status management | Bulletin board |
My approval |
Performance statistics |
Reference room |
Favorites |
Report |
Mobile Part | |
---|---|
Inspection mode | Other functions |
Sheet inspection mode |
Log-in/out |
Inventory inspection mode |
Attach photo |
Download inspection plan |
QR/RFID |
Upload inspection plan |
|
Shift journal | |
Search shift journal |
|
Expectations
-
Enhanced work efficiency
Increased work convenience through automatic task assignment and mobile inspection according to the inspection cycle
Minimize work errors and reduce work load by computerizing inspection work
Objective equipment/operation inspection : Prevent human errors
Paperless work environment
Improved satisfaction level among field workers and managers
-
Activate information sharing
Automatic generations of various reports through the system
Send daily report email
Reduced workload and management costInspection/result data can be converted into a database that can be shared real-time between related departments to be utilized in various analysis
-
Enhanced quality level of equipment inspection
Ensured data accuracy and improved inspection efficiency
Improved equipment operation availabilityPrevention of equipment risks through standard value setting, early warning rule setting, alarm setting, etc.
-
Work standardization
Standardization of inspection process
Standardization of inspection items, cycles, units, and methodsEnhanced reliability through inspection process standardization
Establishment of an advanced system in terms of cost-effectivenessStandardization of daily inspection at all business sites
Product inquiry
02-555-7401
smart@wezon.com
Alarm Monitoring System
Alarm Monitoring System(AMS)
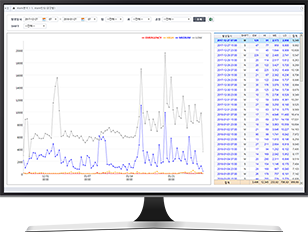
Alarm occurrence trend by importance
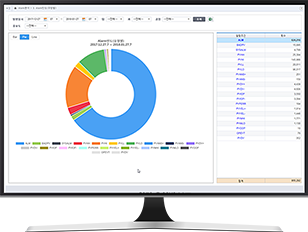
Distribution by alarm type

Alarm Monitoring System(AMS) collects, manages, analyzes alarm data generated from DCS, RTDB, and process monitoring systems and provides the result to users.
The goal of alarm management is to reduce the number of alarms and provide operators with a consistent and stable action event notification interface for safe
and efficient operation.
Main functions include alarm frequency monitoring, multivariate analysis, alarm time management, trend in alarm occurrences by importance, alarm generation and notification, etc.
Importance
By securing an integrated alarm management system by establishing an alarm monitoring system,
we manage alarms in compliance with the international guidelines and standards of EEMUA 191 and ISA 18.2,
providing an environment where we can focus on alarms related to operational safety/loss, and thereby contributing optimal
process operation and safe operation.
System
configuration
diagram
Key functions
Alarm frequency |
---|
Alarm flood |
Alarm occurrence rate |
Top 20 Bad Actors |
Repeated alarm |
Alarm status |
Importance distribution(by setting) |
Importance distribution(by occurrence) |
Hold alarm |
Alarm standard change history |
Alarm time management/Other indicators |
---|
Long-term alarm(24 Hours) |
Alarm responsitivity analysis |
Operator event frequency |
Alarm vs Event |
Alarm statistics |
Stand KPI indicator |
ANSI/ISA18.2 |
EEMUA191 |
Hold alarm |
Alarm collection(DCS) |
---|
Yokogawa |
Azbil |
Emerson |
Metso |
Honeywell |
Serial / OPC A&E |
Basic information |
Tag |
Plant |
Boardman Group |
Expectations
-
Supports systematic management and enhanced operational safety and productivity
Supports systematic management of alarm information and enhanced operational safety and productivity
-
Establishment of internal standard
Establishment of internal standard for alarm management
-
Management upgrade
Upgrade in alarm management method
-
Streamlined data management
Streamlined alarm data management
-
Analysis and support
Support for alarm analysis work
Product inquiry
02-555-7401
smart@wezon.com
Multivariate Analysis Mate
Multivariate statistics procedure analysis system MVAmate
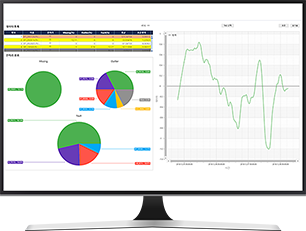
Data pre-processing and statistics
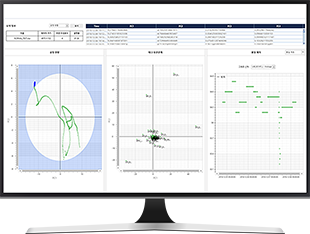
Procedure status analysis and prediction through modeling
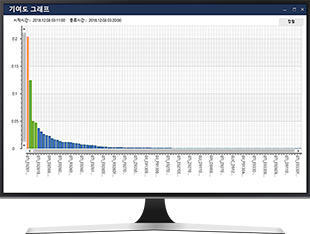
Cause analysis for abnormalities
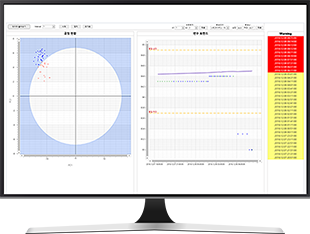
Online monitoring and alarm system through
real-time data analysis
Multivariate statistical process analysis systems are algorithms that can be used to extract important information from large multivariate data sets, such as plant data.
MVAmate uses statistical methods to provide users with information on current and past process status using information collected through sensors in the process.
Main functions include process data statistics through data preprocessing, process status monitoring, alarms for abnormalities, and cause analysis.
Importance
-
01
Enhanced productivity
Increased production continuity through early detection and actions on equipment abnormalities
Production management based on objective data
Increased productivity by producing uniform quality products
-
02
Real-time monitoring
Improved predictive/preventive maintenance capabilities through real-time monitoring
Improved problem analysis and response capabilities
Immediate identification of abnormal data
-
03
Objective quality analysis
Identify causes of changes in process quality, process capabilities and status
Comparison of data characteristics by factor
Comparison of data trends through various graphs
System
configuration
diagram
Key functions
Data |
---|
Load excel data |
Edit excel data |
Export excel data |
Connect process data |
Process data group(by tag) |
Data Explorer |
Data standardization |
Missing data analysis |
Fault Sensor analysis |
Analyze outliers |
Analyze trends |
Analyze by group |
Modeling |
---|
Modeling |
Process Condition Analysis(PCA) |
Quality Prediction Analysis(PLS) |
Data analysis |
Tag correlation analysis |
Process deviation score |
Tag contribution analysis |
Trend analysis |
Analysis by group |
Monitoring |
---|
Model monitoring |
Real time process status |
Real time quality prediction |
Data analysis |
Tag trend analysis |
Real time alarm |
Abnormal status alarm |
Real time data connection |
System management |
Preprocessing algorithm setting |
Modeling control level setting |
User management |
Expectations
-
Improved data quality
Diagnose abnormal sensors through diagnosis on lost data, broken sensor data, etc.
Improved data quality through correction of abnormal data such as lost data, outliers, data noise, etc.
-
Detect abnormality through dimensionality reduction
Reduced data dimensionality through data analysis and modeling
Detect abnormal data in reduced dimensions and analyze the cause of abnormalities
-
Data correlation analysis
Correlation analysis between process variables through Principal Component Analysis(PCA)
Correlation analysis between process variables and quality variables using Partial Least Squares(PLS)
-
Real-time data monitoring
Apply real-time data to models built on existing data
Detect process deviations through real-time monitoring within the model
Product inquiry
02-555-7401
smart@wezon.com